
PIDAnalytix.COM
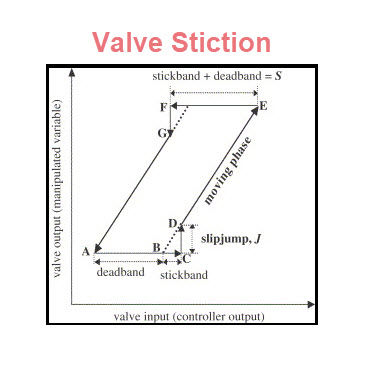
Stiction is an inherent physical/mechanical characteristics of a control valve including process environment. Arguably, it is present in small to large extent in every control valve. It can vary over time due to process conditions changes. Deadband is the root cause of the stiction and therefore for loop oscillations. It is even more insidious than non-linear process gain variations. Attempts to work around this problem has have limited success. For instance, use of two valves, one large and one small for valve position control has been done albeit with limited success but not without its own "tuning problems". A reading of this in the literature would suggest having to deal with tuning of "two" heavily interacting loops. Welcome to more PID tuning problems.
In contrast, as demonstrated herein, AI-PID tuning can mitigate/avoid oscillations caused by varying deadband.
Valve Stiction is a "hidden" process parameter which is even more difficult to deal with than process gain G.
In this demonstration, deadband arising from valve stiction is randomly varied 256 times. Again, a comparison is made of typical PID tuning with AI-PID tuning. In both these two cases, AI-PID performance remains stoically same, the variations of process parameters are fully and perfectly compensated.
There is no known demonstration in last 100 years of PID tuning of such wide variations and perfect control.
Welcome to witness a new dawn of AI-PID tuning to marvel at what can be done with mighty PID. Incidentally, simplicity of PID as a controller is what underlines adaptability of AI-PID. AI-PID demonstrates enduring power of PID arising from its simplicity.